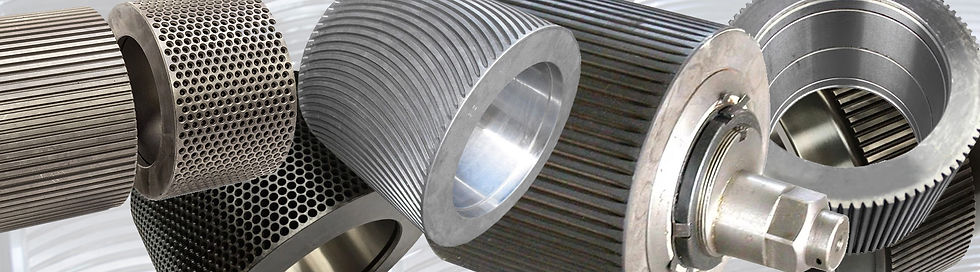

Rollers and shafts for pellet mills and pelletizers
Rollers manufactured by Nawrocki Pelleting Technology are the result of forty years of experience in pelleting, mechanical and thermal processing. We supply roller shells, complete rollers and accessories for the all users of pellet mills. Our rollers are designed for pellet mills with manual roller adjustment and by means of a remote adjustment system.
Specification of rollers for pellet mills and pelletizers
Technical information for the rollers we produce in our factory in Żnin
Certified steel 100Cr6,
Repeatable CNC quality,
High mechanical strength,
High abrasion resistance,
Failure rate below 0.5%,
Orecision of execution on CNC machines,
Production time up to 5 days.


NPT is a manufacturer of rollers for all kinds pellet mills
What are the characteristics of the rollers for pellet mills and pelletizers supplied by NPT? The company's forty years of experience in the production of these components translate into unique technological and material solutions that are responsible for their efficiency and durability.
Production technology of rollers and shafts for pellet mills and pelletizers
NPT specializes in the production of rollers and shafts that are not only effective, but also highly durable, thanks to the use of processes such as machining, hardening and CNC grinding. It is this precise machining, using advanced CNC centers, that ensures reliability and the highest quality of manufactured elements. Additionally, the company uses both traditional and induction hardening methods, which increase resistance to wear and mechanical damage. Thanks to this, Nawrocki products are able to withstand even the most demanding working conditions in various industrial environments.
Rollers and shafts for pellet mills and pelletizers: curved, straight and with holes
Nawrocki offers various types of rollers, including arched, hole and straight, which can be adapted to the specific needs of pellet production. The company also offers special rollers, designed to individual order, which allows the product to be adapted to the specific requirements of the customer, both in terms of dimensions and technical parameters.
Quality control of rollers and shafts for flat and ring dies
Quality control is an integral part of the production process in our company. Each production batch undergoes rigorous testing, including measurements of hardness, dimensions, and the quality of the work surface. Thanks to this, customers receive products that are not only reliable, but also comply with the highest industry standards.
Production of rollers for pellet mills
We manufacture the rollers in our factory in Żnin, Poland. We have a complete machine park for machining and 2 heat treatment stations with four hardening furnaces.
01
The raw material from which we produce the rolls is first roughly turned on a conventional lathe and then turned on CNC centers, where we also perform threading and other operations in accordance with the documentation.
02
The turned forging then goes to the milling department, where the tread is created – the working surface: arc, hole, straight or slanted. On special request, we also make mixed treads.
03
Then we mark it with an individual number and harden the roll, first the outer surface, then the inner surface. After hardening, we temper the roll to obtain the correct parameters. We also harden it using the through-hardening method.
04
After full heat treatment, the internal surface is turned and then ground (on grinders, not lathes) to obtain a perfect finish for bearings.
05
The finished roll goes to the warehouse, where we store it in appropriate conditions.
All production is carried out in accordance with the ISO 9001: 2015 standard.
Quality control of rollers and shafts for pellet mills
Quality control of roller shells
All roller shells manufactured by NPT undergo a control procedure. Each shell is given a unique number, which allows for full identification of the steel and the production process.
Quality control includes
-
hardness of the inner and outer surfaces,
-
dimensions of individual sections and surfaces,
-
smoothness of the grinding of the inner surface under the bearings.
The quality of our rolls is proven by our Clients, who include the largest feed producers in the world. They have trusted our technology, confirmed the quality and punctuality. By joining them, you receive a guarantee of reliability and satisfaction.
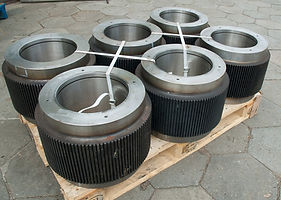
Regeneration of rollers and shafts for pellet mills and pelletizers
Our comprehensive service ensures the highest quality and timely deliveries. Therefore, in addition to roller shells, we supply a complete set of roller accessories: eccentrics, bearings, covers and seals, as well as lubricants.

Regeneration of rollers and environmental protection
We dispose of used rollers, bearings and lubricants in accordance with internal ISO 14001 Environmental Management Systems procedures. We clean all roller elements in cold cleaning machines. Used cleaning cloth is periodically replaced by our supplier and safely degraded with respect for environmental protection principles.
Redesign of the rollers
We all know that simplifying reduces failures and costs. That's why we offer redesign of rollers that are problematic in design. This often involves a complicated and outdated sealing system or lid attachment.
When changing the raw material, it is often recommended to also change the working width of the roll. And here we come to help in determining the optimal parameters of the rolls, as well as flat and ring dies.
