Vibrating screens for pellets and granulates
Granulates and pellets without impurities
Cleaning the granulate from unwanted crumbs and dust is a necessary process to obtain the highest quality granulate of any type. It is extremely important to remove dust from the granulate mass, which in certain conditions can be the cause of an explosion and require additional expensive explosion-proof solutions
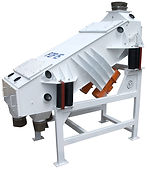
Advantages of our vibrating screens
Flexibility of pellet and granulate cleaning tasks
Capacity from 1 t/h to 30 t/h,
Possibility of using 1, 2 or 3 sieves,
Up to 3 size fractions depending on the production technology,
Additional 4th fraction for large waste (lumped feed or other raw materials); discharged into a separate container.
High efficiency of granulate cleaning and screenings removal,
Gravity discharge or pneumatic conveying system,
Aspiration system for dust to the central filter or Dust Return and Dosing System (DRDS)
Construction and equipment of screeners
A flow guide that eliminates the unfavorable supply of raw material through the pipeline at an angle to the feed,
The thickness flap of the screened raw material allows for even distribution of the raw material over the entire width of the body before it is fed onto the sieve,
A series of inspection glasses for manual sampling and control of the sieved fraction,
Two vibrators with full adjustment of vibration force, adapted to the required operating parameters,
Vibrators mounted parallel from below on a strong welded base (20mm sheet metal),
Springs selected for highly efficient screening of all types of granulate (pellets),
Spring bases attached to the frame on centering discs, which can be easily installed on the existing frame,
Standard or custom designed strong support frame, depending on available height,
Individual design of outlets for individual fractions (biomass and other raw materials) is possible.
Quick replacement of sieves in PZP screeners
Easy access to tensioners at the rear of the screens,
Quickly removable large covers across the entire width of the screen,
Hooks released manually, without the use of additional tools,
Simple design and easy to use screen tensioning based on the drum-arm principle.
Gravity Return and Screening Dosing Team - DRDS
Controlled and even % dosing of screenings to the conditioner screw feeder (recommended),
No risk of uncontrolled dust filling of the granulator (blockage possible),
A tank with a capacity of about 1m3 with a structure, selected individually; two Endress+Hauser level sensors (bottom and top),
Complete set of metal pipelines and connectors,
Individually selected parameters of the screw conveyor receiving the screenings (one or two inspection hatches, overflow/blockage sensor),
Individually selected parameters of the screw feeder and the size and shape of the discharge,
AIAC compliant.
Pneumatic Return and Dosing System for Screenings
Designed especially for factories producing pellets from biomass and other raw materials,
Efficient recycling of screenings to the central dust filter (usually a pulse filter),
The screw feeder behind the filter lock transports dust with controlled efficiency to the selected device (depending on the configuration and technology of the given production line).
Technical data of NPT pellet and granulate screens

Przesiewacz PZP-15

Przesiewacz PZP-15

Zbiornik odsiewek

Przesiewacz PZP-15
What is the significance of granular material screening technology for modern production processes? In the dynamically developing industrial sector, where efficiency and precision play the most important roles, advanced solutions are becoming an indispensable element ensuring the highest quality of products. Among the companies that lead in innovation is NPT Nawrocki. We specialize in the production of vibrating screens, which determine the strength and reliability of production processes in many industries.
Vibrating screens for pellets and animal feeds
Is there a more innovative technology in the biomass and feed processing industry today than vibrating screens? Without a doubt, NPT Nawrocki answers this question through its innovation and adaptation to growing market requirements.
Our vibrating screens are characterized by significant capacity, ranging from 1 t/h to 30 t/h, which makes them suitable for various production scales. Thanks to the possibility of using from 1 to 3 sieves and the flexibility to segregate the material into up to four different fractions, these devices are ideal for plants processing both small and large quantities of raw material. A special fourth fraction allows for the separation of larger waste, which is necessary in the processing of lumpy feed or other lumpy raw materials.
Each element of the screen construction has been designed with the optimization of processes and the maximization of efficiency in mind. From the stream guide, through the thickness flaps, to the advanced aspiration and screenings discharge systems – NPT Nawrocki ensures that every detail promotes reliability and efficiency of work. Two vibrators with adjustable vibration force and springs adapted to different types of granulate are just some of the functions that raise the standards of use.
Our company does not limit itself to the production of screens. As a general contractor of pelletizing technology, Nawrocki offers comprehensive solutions for production lines – from design, through delivery, to start-up and automation of the line. Project management, explosion hazard assessments (ATEX) and construction supervision are integral elements of the offer, which provide customers with peace of mind and a guarantee of trouble-free operation of the plants.