
Industrial Screw Conveyors and Feeders NPT
We produce screw conveyors for dosing and transporting bulk raw materials (grains, feed, biomass, RDF and others) with capacities ranging from 0.5 t/h to over 35 t/h.
We manufacture conveyors in trough and tubular versions. They are also made in versions for the EX22 and EX21 zones and with a wide range of optional equipment.
NPT screw conveyors for special applications for feed, biomass, plastics, sewage sludge

Conveyor belts for various raw materials and temperatures
When designing a screw conveyor, we take into account the unusual properties of raw materials, such as bulk density, temperature, abrasive properties, and others. We select appropriate components that will withstand the impact of the raw material on the internal components of screw conveyors.
Abrasive Materials
Abrasive materials can cause excessive wear to the trough and conveyor components. They should be conveyed at slower speeds and with less loading on the trough. For very abrasive materials, it may be necessary to use thicker screws and troughs, surface hardeners, or special alloy components.
Chemical raw materials
Chemicals and food additives, require sealed end bearings and nylon or other dry running suspension bearings. Trough covers are sealed, closed and easily removed for frequent cleaning. Internal welds in contact with the raw material may require polishing to eliminate material retention.
Degradable materials
Materials that tend to fall apart or separate should be conveyed in large diameter conveyors at very slow speeds to minimize physical shock to the material.
Extreme temperatures - cooling jacket
Conveyors handling materials at extreme temperatures should be constructed of metal alloys designed to operate under these conditions. Highly corrosive materials combined with high temperatures require special consideration in alloy selection to maximize component life. It may be advisable to use jacketed troughs, in which a heating or cooling medium can be circulated to maintain the conveyed material at safe operating temperatures. Conveyors handling hot materials also experience thermal expansion and will increase in length as the trough and screw temperatures increase after the hot material begins to be conveyed.
Materials creating explosive atmospheres EX
The conveyor must be designed with non-sparking and explosion-proof components and must be sealed. An exhaust system for ventilation may be necessary if hazardous dust is present.
Swelling materials
When conveying materials that tend to aerate and swell, the size and speed of the conveyor must be designed based on this larger swelled volume and density. Such materials will often pass through the gaps around the screws. In these types of screw conveyors, low speeds, small gaps, and special screw edges must be used.
Hygroscopic Materials
Hygroscopic materials readily absorb moisture and tend to become denser and more difficult to flow. Sealed conveyors that exclude the outside atmosphere are effective in handling these materials.
Mixing During Transport
When mixing of base material with additives is required, a conveyor consisting of screw ribbons, cut and folded screws, cut feathers or blades can be used, individually or in any combination to achieve the desired effect.
Moving at an angle
Inclined screw conveyors have a higher power requirement and lower efficiency than horizontal conveyors. The level of power increase and actual efficiency depends on the angle of inclination and the properties of the conveyed material.
Sticky or Sticky Materials
For these types of raw materials we use ribbon conveyors to minimize material build-up.
CONSTRUCTION
semicircular U-shaped trough
semicircular trough V
square trough
pipe trough made of pipe
combined pipe trough
insulated trough
trough with water jacket
TEMPERATURES
atmospheric 5-35C
increased to 120C
high above 120C
Execution:
thermal insulation
thermal insulation with electric heating
steel jacket with heating or cooling medium circulation
CONNECTIONS
Pour:
square
rectangular
round
collar for reduction, connector
Dump:
square
round
SENSORS
ATEX
temperature
vibrations
Other
level on the island
shaft revolutions
dump locks
ATEX explosion-proof design of screw conveyors and feeders
In accordance with the Explosion Hazard Assessment, which defines the EX zone, we equip screw conveyors with appropriate solutions in accordance with the ATEX Directive.
For the EX21 and EX 22 zones we use temperature and vibration sensors. In the frequent case of grounding necessity, we use equalization connections between individual conveyor sections.
For the EX20 zone we design the conveyor individually. Determining the parameters for work in this zone requires consultation with the OZW/OZZ contractor and raw material tests.


For outdoor work
Screw conveyors with double slope cover
For outdoor use, we recommend screw conveyors with a modified cover with a gable roof.
Thanks to it, water and snow flow off the surface of the cover by gravity and do not expose the sheet metal to the influence of unfavorable factors.
In the case of snow or ice that can form a heavy layer, it is important to remove them quickly, especially on screw conveyors installed at heights with difficult access, especially in winter.

Wybierak ślimakowy spod wagi; stal konstrukcyjna, koryto U.
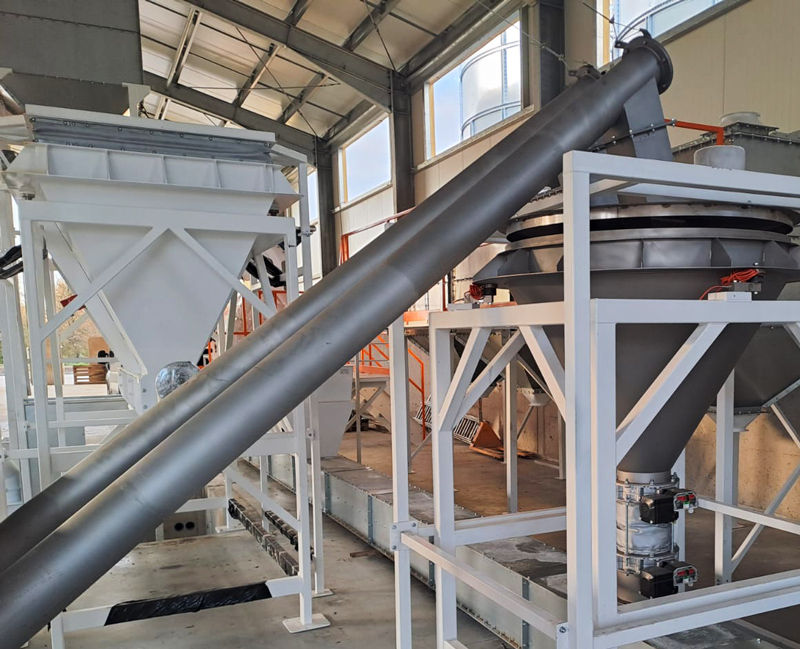
Dozowniki ślimakowe komponentów; stal KO, rurowy.
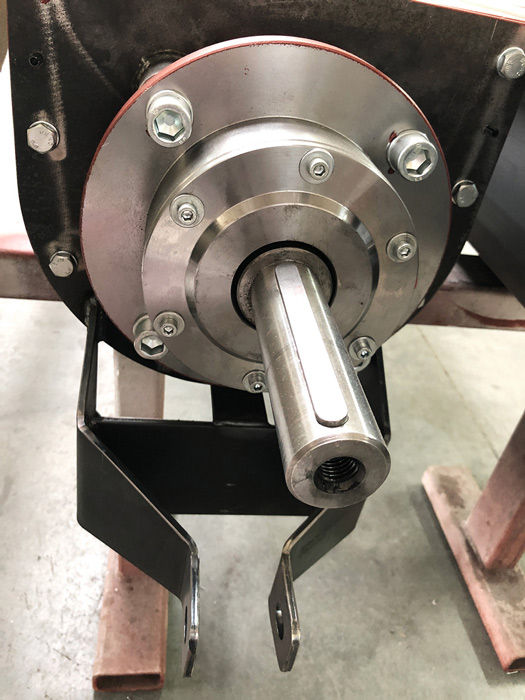
Obsada łożysk (własna konstrukcja, galwanizowana)

Wybierak ślimakowy spod wagi; stal konstrukcyjna, koryto U.
Feeders and screw conveyors for grain and bulk materials
In the era of rapid technological development, the manufacturing industry worldwide is facing new challenges. Operational efficiency, process safety and environmental protection are the most important criteria that modern transport systems must meet. In this context, technologically advanced screw conveyors play a special role, exceeding the traditional functions of transporting raw materials, becoming an indispensable element in complex production processes. NPT Nawrocki, a leader in granulation technology and pellet production, offers innovative screw conveyor solutions that are designed to meet all these criteria. These conveyors, used in various industrial sectors, from chemistry to biomass, are an ideal combination of reliability, efficiency and ecological responsibility.
Screw conveyors in the NPT Nawrocki offer
What are the technical and engineering challenges of designing screw conveyors that must meet the specific requirements of diverse industrial environments? NPT Nawrocki, known for its innovative solutions in granulation and pellet production technology, offers a wide range of screw conveyors designed to meet these challenges.
NPT screw conveyors are available in trough and tubular versions, which allows for flexible adjustment to the specific process needs of various materials - from grain to biomass and chemical materials. The use of special components such as sealed bearings and easily removable covers facilitates maintenance of cleanliness and safety, especially important when working with chemicals and food additives. In turn, for degradable materials, such as some types of biomass, conveyors are designed to operate at low speeds to minimize mechanical damage to the raw material.
The company also pays special attention to the safety of operation in environments with a risk of explosion (EX zones), using explosion-proof components and extraction systems in places where there is a risk of accumulation of dangerous dust. Additional equipment, such as cooling and heating jackets, ensures optimal operating conditions of conveyors in extreme temperatures, which is important when transporting materials that react to temperature changes.
Dozowniki i przenośniki ślimakowe do surowców sypkich to kluczowe elementy w procesach produkcyjnych, gdzie precyzja i niezawodność są na wagę złota. Nasze urządzenia zostały zaprojektowane z myślą o maksymalnej wydajności i minimalizacji strat materiałowych. W celu zapewnienia niezawodnej pracy urządzeń, oferujmy również kompleksowy serwis peleciarek, który obejmuje przeglądy i konserwację fabryk pelletów.
W produkcji pasz, dozowniki i przenośniki ślimakowe do pasz odgrywają kluczową rolę, zapewniając równomierne i dokładne dozowanie składników. Innowacyjne technologie zastosowane w naszych urządzeniach zwiększają efektywność produkcji i ułatwiają zarządzanie procesami.
Transport zboża wymaga specjalistycznych rozwiązań, które zapewnią bezpieczeństwo i integralność przewożonego materiału. Dozowniki i przenośniki ślimakowe do zboża oferowane przez NPT Nawrocki spełniają najwyższe standardy jakości, co gwarantuje bezpieczny transport nawet najbardziej wymagających surowców.
Niezawodność w produkcji to cecha, którą cenią sobie wszyscy nasi klienci. Przenośniki ślimakowe NPT Nawrocki zostały stworzone z myślą o zapewnieniu ciągłości pracy w różnych gałęziach przemysłu. Dzięki zastosowaniu najnowszych technologii oraz wysokiej jakości materiałów, nasze urządzenia są niezawodne w produkcji, przemyśle, rolnictwie.
Charakteryzują się wyjątkową trwałością i odpornością na intensywne użytkowanie. Nasze dozowniki i przenośniki ślimakowe do surowców sypkich to odpowiedź na potrzeby nowoczesnego rolnictwa, oferując niezawodność i efektywność w codziennych operacjach.