
Granulation lines for the production of pellets from sawdust and wood chips.
Since 1998, we have been designing, manufacturing and delivering complete production lines for pellets from forest and agricultural biomass.
We specialize in capacities from 2 t/h to 6 t/h, ATEX explosion-proof design, with fully automatic control.
We subject forest biomass to appropriate mechanical and thermal treatment depending on its original size (trunks, boards, wood chips, sawdust) and humidity level: we dry or moisturize and refine it.
Sawdust pellet lines
The following processes occur in the wood chip and sawdust pellet factory:
coarse grinding, pre-grinding and final milling,
drying in drum or belt dryers,
granulation in ring or flat technology,
enrichment with powdered or liquid modifiers,
cooling, cleaning, dust elimination,
packing in bags, big bags or shipping silos.
Download the catalogue on pelleting forest biomass
File (0.5 MB) >>>
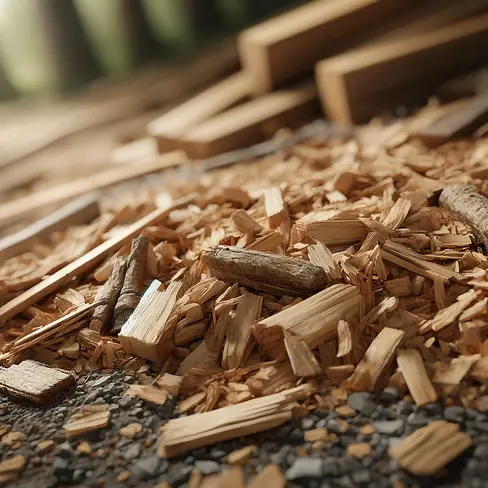
Stages of producing pellets from sawdust and wood chips
Coarse and preliminary grinding of sawdust
Chipper and hammer mills for wood chips and sawdust
-
If the primary raw material is tree trunks, boards, wood chips or similarly sized forest biomass, we use the following processes:
-
For coarse shredding, especially of tree trunks, we use powerful chippers with a power of up to 150 kW - 200 kW. The product of these chippers is chips of 60 mm - 100 mm in size, which require further shredding, as they are not yet suitable for granulation.
-
Pre-grinding prepares the raw material for heat treatment in the dryer. The highest drying efficiency is achieved for fractions of 10 mm - 20 mm.
-
This process takes place in shaft or beater chippers equipped with sieves adapted to the required final parameters of the granules.
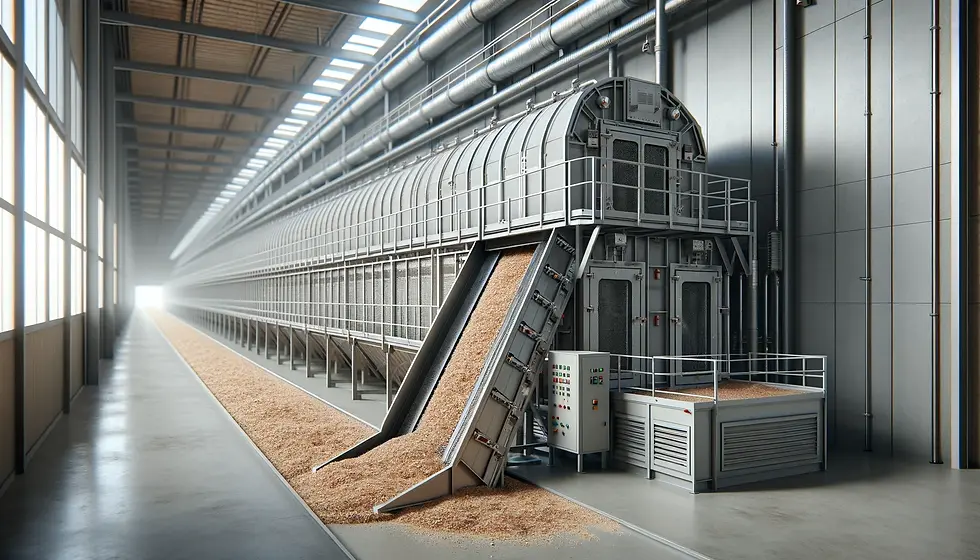
This process requires prior crushing of the raw material into sawdust or needles measuring 10 mm - 20 mm. Thanks to this, drying efficiency is the highest, because the drying agent can penetrate deep into the raw material particles, reducing the moisture level from 55% - 60% to the desired 10% - 12%.
We use drum dryers (up to 2.5 t/h) and belt dryers for higher capacities.
We supply dryers complete with a cyclone station, fans, a raw material tank, a fuel production system and a feeder furnace. The equipment varies depending on the type of dryer. We recommend using moisture meters that continuously monitor humidity and automatically regulate the raw material flow.
We secure the drying process using spark detectors, temperature sensors, sprinkler systems and automation that cooperates with the central control system of the entire factory.
Drying wet sawdust and ground wood chips
Grinding of sawmill waste
An essential step in preparing the raw material for granulation is the standardization of particle size, which is necessary to produce high-quality granulate and reduce the amount of dust.
The rotating hammers of the hammer mill, in addition to reducing the fraction, crush the chips, open the pores and fiber structures. This facilitates the penetration of water or water vapor, which results in better compaction of the raw material in the matrix holes and higher factory efficiency.
Moreover, appropriate grinding softens the lignin fibers, eliminating the need to add additional, expensive binders.
The regrinding is pneumatically assisted by a fan and cyclone system, which create negative pressure in the expansion chamber. This increases the efficiency of the system by at least 30%, which is consistent with NPT's energy-efficient production systems.
Conditioning and Granulation of Sawdust
The target process is granulation, which takes place in dedicated GR type industrial granulators with a reinforced structure for high-performance production of high-quality pellets.
In the granulator, the pre-prepared raw material is compacted, but not only, by its appropriate grinding.
Previously, just before the pelleting chamber, the raw material is soaked in water or steam in a conditioner, which is required for professional pellet production.
The key element is the die and rollers. The die parameters are adjusted to the specific raw material. A die for softwood will not produce hardwood pellets and vice versa.
Nawrocki PT granulators guarantee efficient operation only if their parameters are properly selected for the raw material. Consultation with our technologists is essential.
ATEX
SECURITY
EXPLOSION-PROOF
Cooling of sawdust and straw pellets
Counterflow coolers have 4 tasks to fulfill: reducing humidity, increasing mechanical strength, increasing the energy value and lowering the temperature of the granules.
After leaving the cooler, the pellets are ready for cleaning in a vibrating screen because they are already hard enough and will not be damaged mechanically. In addition, they become a full-value fuel with a high calorific value.
Our coolers combine compact design with innovative solutions that protect the production line and the Investor. The coolers do not require any special source of coolant, because it is air from the factory or outside, supplied through a separate channel.
The retention time of the granulate in the cooler can be freely adjusted from the central computer.
Cleaning pellets from sawdust
After cooling, the granulate acquires high mechanical strength and can be subjected to final cleaning in a vibrating screen.
The screener separates unwanted crumbs, dust and small pieces of granules and directs them to the pneumatic conveying system, which returns them back to production - nothing goes to waste.
The clean granules are gently stored in the granulate tank from where they are then sent for packaging or dispatch.
Dust and screenings (also from other devices) are pneumatically transported to the dust filter, which collects them and returns them to production through an aspiration lock. This keeps the production hall clean, reduces the risk of explosion due to excessive dust, and allows bearings and other machine components to operate without failure for longer.
Storage and packaging of granules
Clean granulate (pellet) can be stored in a flat warehouse (e.g. straw granulate), dispatch silos or in granulate tanks - it depends on the method of distribution: loose or packed.
Pellets are packed in 5 - 10 - 15 - 25 kg bags in automatic or semi-automatic weighing and packaging machines or in big bags with a capacity of 0.5 or 1 tonne.
For capacities up to 2.5 t/h we use semi-automatic weighing and packaging machines, and above that we recommend automatic machines. Pellet factories with capacities above 7 t/h should also have a palletizer to fully automate the packaging process.
Request for quotation form:
What elements allow a technology company to succeed in today's rapidly changing world? Undoubtedly, these are innovations, adaptation to changing market needs and the ability to predict future trends. In the field of feed and biomass production, NPT Nawrocki stands out as a leader that not only follows these trends, but also actively shapes the future of the industry. With deeply rooted experience dating back to the 1970s, we perfectly combine tradition with modernity, providing solutions that are both innovative and reliable. The use of advanced technologies in the design and implementation of comprehensive production lines for feed granulation and biomass pellet production raises the standards of efficiency, safety and environmental protection.
Pelleting lines for the production of pellets from sawdust and wood chips
How do modern technologies contribute to more efficient feed and biomass production? NPT Nawrocki, with a rich history of innovation and experience dating back to the seventies, sets standards in the field of feed granulation and biomass pellet production. As a pioneer in this industry, we are constantly modernizing our processes to meet the latest technical and legal requirements, offering solutions that are not only effective but also environmentally friendly.
NPT Nawrocki specializes in designing, manufacturing and delivering complete production lines for a variety of raw materials - from animal feed, through forest and agricultural biomass, to plastics and sewage sludge. These lines are tailored to the specific needs of each customer, ensuring flexibility in production and ease of subsequent expansion. This approach not only increases operational efficiency, but also contributes to reducing operating and maintenance costs.
NPT Nawrocki offers a wide range of machines for the granulation line, including granulators, coolers, screeners, crushers and sterilizers. Each of these machines is designed to operate in a potentially explosive atmosphere, which is essential in risky industries such as feed or biofuel production. The company also conducts a detailed Explosion Hazard Assessment for each project, ensuring the safety of both the production process and the employees.
Machines for producing pellets from hay and wood chips
NPT Nawrocki's innovation is also reflected in the use of advanced software for designing machines and factories, which enables precise adjustment of production lines to individual customer needs. The projects implemented are characterized by a high degree of automation, which reduces production costs and increases its efficiency. The use of modern solutions, such as conditioning systems, which prepare the raw material for granulation, or comprehensive cooling and dust removal systems, ensures the production of high-quality pellets, compliant with international standards such as the DIN+ standard.
Each project carried out by NPT Nawrocki is not only a delivery of machines, but also a comprehensive service covering technological design, construction and supervision over the correct execution and launch of production lines. Thanks to this, the company's clients can focus on developing their markets without worrying about the technical aspects of production.