What is granulation and pelleting.
Granulation Compaction Densification
Granulates and pellets: the same, but for different raw materials
Compaction or densification technologies, also known as densification through granulation, are becoming increasingly widely used in many industrial sectors.

What is granulation - pelleting?
Granulation and pelletizing consist in gluing the raw material particles together during compression at high temperature in the holes of the granulator matrix. Regardless of the type of matrix – ring or flat – the quality of the granules depends on the strength and durability of the bonds between the raw material particles. It is influenced by the appropriate selection of matrix parameters for the composition of the raw material, matrix temperature, pressure, any binder and previous thermal treatment of the raw material.
Granulated raw materials have a number of advantages:
easy to precisely dose,
low transportation costs,
low dust level,
permanent composition,
stable physicochemical parameters.
The quality of granulate and the efficiency of the production line are greatly influenced by the entire technological area, which consists of individual functional production subsections related mainly to dosing, weighing, grinding, refining, mixing, conditioning, sterilization, hardening and humidity reduction, cleaning and packaging.
Granulation and pelleting consist of 3 basic stages:
Individual raw material particles are transformed into a compact mass of constant composition and parameters, in which most of it retains its original properties. The mass energy is dissipated by intra-particle friction and friction of particles against walls.
In the second stage, the raw material particles are pressed together and their mutual interaction is significantly increased. Then the plastic deformation process begins, which takes place in the granulator matrix. The particles are connected by electrostatic forces and van der Waals forces (interactions between a permanent and an excited (induced) dipole).
In the final stage, the volume of the raw material is reduced, which results in an increase in the density and bulk mass of the raw material, now in the form of granulate.
During granulation, about 40% of the granulator power is used to compress the raw material , and the rest to overcome friction during compression. Adding the right amount of water to increase humidity reduces the total power required for granulation. That is why our GR series granulators are equipped with conditioners with the possibility of connecting a water installation or a Steam Reduction and Stabilization Unit.

Factors influencing the granulation and pelleting process
>> Variables related to granulation and pelleting processes
:: Temperature
The resultants of granulate quality are density and strength, which are significantly influenced by temperature. At a constant and appropriate raw material moisture level, increasing the temperature lowers the minimum power required to form granules. In addition, the appropriate process temperature affects the stability of their density and size.
It is important to select the matrix in such a way that the degree of accumulation does not exceed the established values, because then the granules will burn or even ignite. The raw material is heated to the optimum temperature in the conditioner using dry steam generated in a steam boiler (see Steam Reduction and Stabilization Unit).
:: Pressure
During granulation, the rollers press the raw material into the die holes with an appropriately selected pressure. The pressure force depends mainly on the raw material, the diameter of the holes in the die and the power of the granulator. From the point of view of the construction of the die and rollers, their working width changes adapted to the size of the granulator, which is of fundamental importance for the efficiency of the process.
GRP and GRB granulators can operate with slightly wider dies than the industry standard due to their higher torque. This results in high productivity while maintaining the appropriate granulate quality.
:: Time of holding and calming down
These factors affect the quality of the pellets, due to the processes taking place inside the holes in the die. They are directly related to the pressure and the degree of the matrix stacking. For example, oak sawdust pellets better at lower pressure but a slightly longer holding time, which results in better pellet density. The pellet settling time affects its density and depends on the way the pellet leaves the die, the total length of the die hole and the degree and mode of compression.
The raw material parameters are of fundamental importance. In the case of poor granulation parameters, the granule expands or disintegrates and the surface porosity increases. That is why the longest possible settling time has such an impact on quality. The number of rollers working with the matrix also has an impact on the holding and settling time.
:: Matrix design and rotation speed
Each die, ring or flat, has several parameters that are extremely important for the granulation process, which mainly, but not exclusively, come down to the so-called degree of accumulation. These parameters affect the amount of raw material - i.e. efficiency, and the amount of energy - i.e. power consumption.
The degree of accumulation is determined individually for each raw material composition and humidity and is the ratio of the hole length to the hole diameter. The relationship is simple: increasing the working length of the hole increases the granulation pressure (pressure force and power consumption), while increasing the hole diameter reduces this pressure. These factors affect production costs, which is why selecting the right degree of accumulation is so important.
:: Matrix rotation speed
We mentioned earlier the retention time of the raw material in the die, which depends on the working and total length of the hole and the rotational speed.
This time also depends on the rotational speed of the matrix, which should be relatively low because it influences, for example, the desired glassy surface of the granules.
The die rotation speed and raw material parameters should be taken into account when deciding on the number of embossing rollers, especially in ring die granulators.
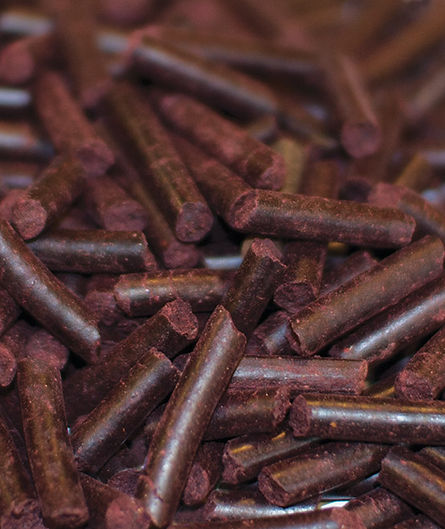
>> Variables related to granular raw material
:: Humidity level
Moisture is crucial in the granule formation process.
In organic raw materials during densification, appropriate moisture facilitates starch gelatinization, protein denaturation and increases the solubility of fibres.
Biomass treated with hot and dry technological steam densifies more effectively because the additional heat modifies the physicochemical parameters that have a positive effect on plying.
Too low or too high humidity results in the production of granules with poor parameters or no compaction occurs at all.
:: Particle size and shape
Generally, the density and strength of granules is inversely proportional to the particle size because smaller particles have a larger contact surface area during compaction.
In addition, the larger surface area facilitates the absorption of water or water vapor added during conditioning, which greatly aids the binding process.
The appropriate particle size combined with a properly selected matrix increases efficiency and reduces power consumption, which lowers production costs.
However, too fine a raw material (e.g. dust) can lead to blocking of the granulation unit, especially in cheap granulators.
:: Type and composition of raw material
-
Knowledge of the behaviour of the raw material during granulation, depending on its composition or recipe and with the participation of supporting factors, is of great importance for the efficiency of the entire production process and for productivity and quality.
-
Pelletizing feed, biomass or other organic raw materials requires adjusting process parameters to components such as starch, proteins, fats, cellulose, hemicellulose, lignin, refiners and binders.
-
Each of these can have a different impact on the final product, and their combination with physical and mechanical processes allows for hundreds of combinations and opportunities for error.

Raw material pre-treatment before pelleting
Preparation of raw materials for granulation plays a fundamental role because it increases the plasticity, efficiency and quality of the final product. The appropriate production process helps reduce electricity consumption and granulate raw materials intended for different groups of recipients.
:: Grinding (grinding, shot blasting)
Before densification, the raw material is ground, most often in hammer mills, although other types of mills, e.g. disc mills, are also used.
This is at least a single-stage process, although in forest or agricultural biomass two- or three-stage crushing occurs.
The particle size determines such features as the sticking characteristics and mechanical properties of the granules.
:: Heat pre-treatment
It is often used because it improves the quality of the granulate by activating binding substances (lignin).
It is most often done in a conditioner or sterilizer. It has an impact on higher efficiency of the production line, which translates into lower costs.
:: Hydrothermal conditioning
This is a less popular technology that involves feeding a special reactor with raw material with hot steam under high pressure. It is used in the feed industry.
:: Torrefaction
It consists of roasting biomass to remove components that cause smoking, increase carbon content and calorific value. Energy pellets are produced from torrefied biomass.
Physical characteristics of pellets and granulates
:: Humidity (%)
The appropriate moisture content of the pellets affects the satisfactory selling price. It results from the calorific value in the case of energy pellets, calorific value in feeds.
Too little humidity contributes to lower profits, as does too much humidity.
Therefore, an effective and precise system for drying raw materials and dosing water or steam is extremely important because it affects the financial results.
:: Bulk density (kg/m3)
This is the mass of the raw material (usually dry) divided by the total volume. It is of great importance for reducing transport costs.
The granulate is ideally suited for packing in bags (e.g. 15 kg) and big bags (500, 1000 kg), which makes its transport much less expensive than the transport of non-compacted raw materials.
High bulk density also means easy dosing and almost complete lack of dusting when properly cleaned, packaged and transported.
:: Mechanical strength index (%)
This is a quality parameter that determines the ability of granulates to be transported and stored in an unchanged state. The higher the score, the better the product.
:: Glassiness
End customers prefer granulates with a smooth and glassy surface than matte and jagged ones. Therefore, it is worth focusing on the production of only the former, because you get more money for them.
Glassiness is a derivative of the density and smoothness of the surface of the matrix holes, therefore it is influenced by the correct grinding of the raw material, the optimal temperature of the matrix and its degree of accumulation, and humidity.
:: Length (mm)
High-quality granulate has a relatively low length tolerance. Depending on the intended use, it is set by adjusting the knives on the granulator die.
Achieving minimal length spread in GR granulators is possible by using up to 3 knives. Even length is important especially for users of pellet boilers.
:: Dusting (%)
Granulates produced at too low temperature and humidity, in poorly selected matrices, have lower mechanical strength.
Dust and crumbs are very undesirable substances, especially in fuel pellets (explosive dust cloud in the fuel tank), and least of all in feed, e.g. rabbit feed.
Dust is created during transportation and storage as a result of mutual friction.
In reducing the amount of dust, the priority is a complete technological process that ensures proper grinding of the raw material, heating and setting the appropriate moisture, granulation, cooling and hardening, and then cleaning in vibrating screens. No production stage should be omitted.
:: Calorific value (MJ/kg or GJ/T)
It is equally important in fuel pellets and feeds, and optimal value is achieved by managing water and steam processes and fat dosing in the case of feeds.
Generally, higher density pellets are more caloric, which requires strong pelletizers that can handle dies with a correspondingly high degree of compaction.
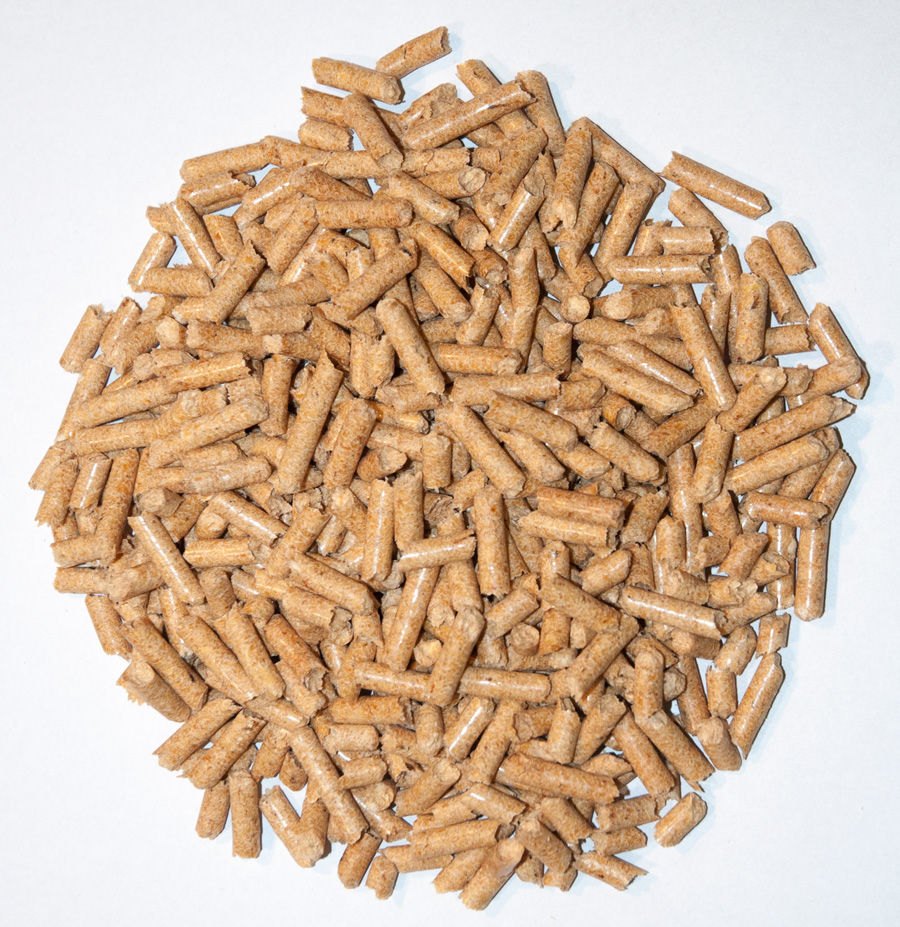