
Industrial granulators up to 320kW for the production of pellets and granulates
Granulators from the GRP series for feed and GRB for biomass and other bulk raw materials
Pelletizing machine - granulator for feed, sawdust, straw, RDF for efficient pellet factories and granulation lines.
NPT GR series granulators do not require operator supervision. They are controlled by a computer. Every minute of operation.
The GR series granulators are safe and easy to use. They meet EU Directives in the field of safety and explosion protection. Health and safety is the most important.
The standard equipment of GR granulators from Nawrocki includes sensors that constantly monitor the condition of critical components.
If the programmed parameters deviate from the norm by even 1%, the computer will perform a programmed procedure that will not damage the granulator.
Operators are protected by mechanical, electronic and procedural safeguards.
Modern technical solutions, as in Western granulators
Granulators from the new GR1 and GR2 series have a wealth of standard and optional equipment. Thanks to them, production efficiency can be increased to a maximum. Similarly, operator safety and comfort of their work have been raised to a higher level. The changeover time of the granulator with QDES.60 has been reduced by 60%, shortening the replacement of the matrix to less than 60 minutes. Granulators from the GRA series are equipped as standard with a remote system for regulating the gap between the rollers and the matrix. In accordance with EU directives, our machines are CE and ATEX compliant.
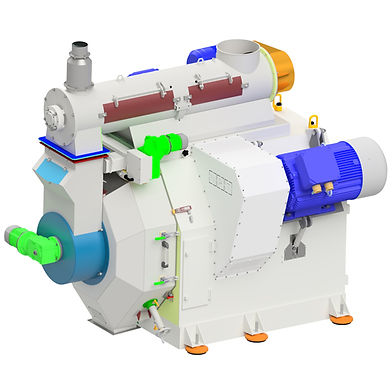

Durable design for efficient production of high-quality pellets from sawdust, wood chips and biomass
Forest biomass requires a pelletizer design with increased mass and strength in order to maintain correct pelleting parameters.
Thanks to the rigid and strong construction, you can produce pellets from the most difficult raw materials such as oak or beech chips.
A large pulley drives the rotating shaft with the torque-generating force you need to achieve performance that meets your business plan.
We guarantee pellet quality in accordance with the DIN+ standard.
Low operating, maintenance and servicing costs. Parts manufactured in Poland. In our factory.
Are production costs important to you? They certainly are and we know that. That is why we have designed machines that are very cost-effective to operate.
-
Thanks to the rigid and strong construction, you can produce pellets from the most difficult raw materials such as oak or beech chips.
-
A large pulley drives the rotating shaft with the torque-generating force you need to achieve performance that meets your business plan.
-
We guarantee pellet quality in accordance with the DIN+ standard.
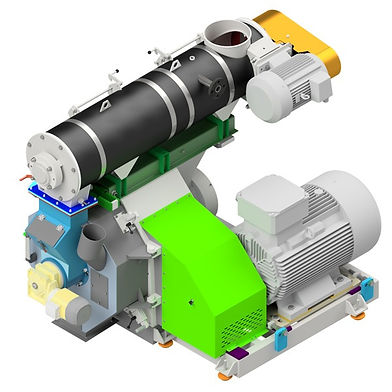
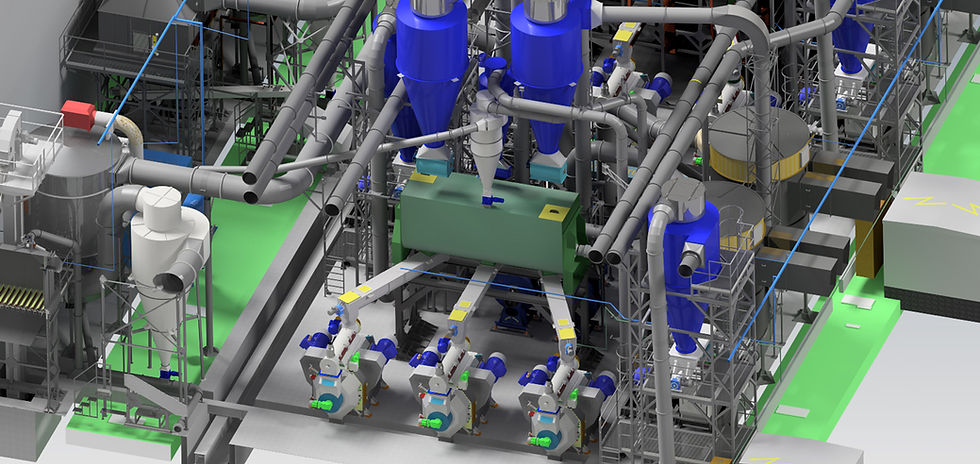
You can't see them. They work in the background. They do a good job.
Technical details are a key element of the mechanical and technological advancement of the granulator. Every detail, from precisely designed details to advanced safety systems, is essential for the efficiency and performance of the device.
01
Granulator body
rigid welded construction, mounted on a frame,
box construction with motors mounted on plates with adjustable height for correct belt tensioning,
a huge standing shaft sleeve with widely spaced bearings increases their service life up to 4 years,
manual or electric lift for mounting the matrix and rollers,
at the back of the door with safety devices preventing access to the drive unit,
body ready to be integrated with a conditioner (or two),
4 or 6 vibration isolators reduce vibrations to a minimum.
03
Assembly and adjustment of the matrix and rollers
standard manual roller adjustment on all granulator models except GRA models,
quick and secure locking of the rollers in a fixed position by tightening the mounting and locking screws,
rigid front roller support mounted on locking screws,
rear roller assembly with 2 scrapers,
2 or 3 scrapers mounted on the front roller mount; full adjustment possible,
a powerful reinforcing ring maintains the rigidity of the assembly and prevents mechanical deformation
a winch or crane integrated with the pellet press body for easy, quick and safe replacement of the die and rollers,
02
Overload clutch
protects the matrix from damage,
reacts quickly if a foreign body gets between the roller and the matrix or if it is overloaded with a sudden increase in amperage,
immediate release of the standing shaft by breaking the fuse attached to the clutch leaf,
easy centering of the clutch with the housing,
quick and easy access from the back of the body,
a groove for a broken fuse allows its easy removal,
simultaneous electrical disconnection of the granulator by breaking the voltage switch.
04
Drive - 1 or 2 engines
GR Nawrocki granulators are equipped with Single or Double Direct Drive (SDD or Double Direct Drive - DDD). Through direct connection by drive belts, the granulation unit receives enormous force, which allows granulation of very difficult raw materials with expected efficiency.
6-pole motors, slow speed 980 rpm. Class IE3
The drive unit is based on a massive rotating shaft sleeve mounted in a welded housing. The sleeve allows for a large bearing spacing, which reduces pressure and extends their service life.
20% larger, powerful main pulley receives the full power of the engines via more V-belts.
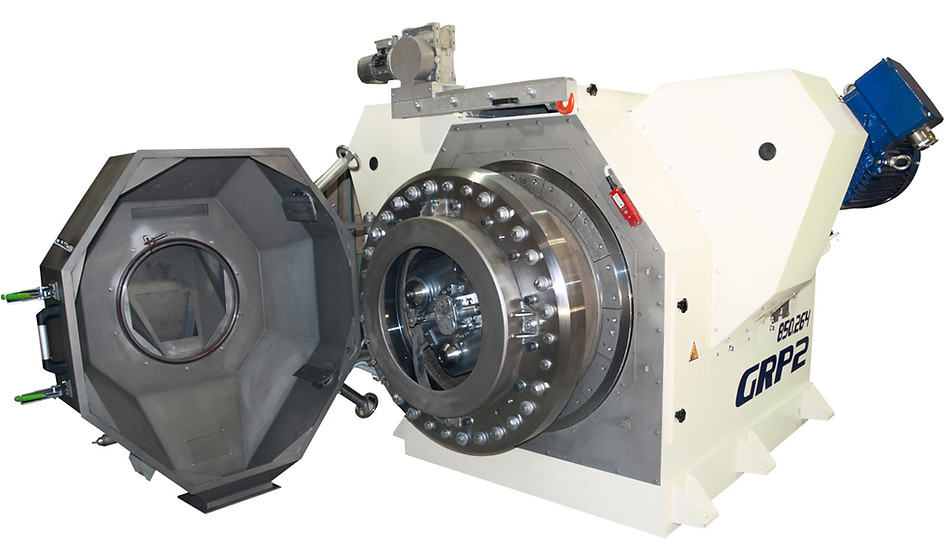
>> GR Granulator Model List
Standard equipment of granulators
Pelletizing press with main drive (1 or 2 motors),
stainless steel conditioner with drive,
1 ring die and 2 or 3 complete rollers,
central automatic lubrication system,
internal pneumatics control system,
electrical/signal box
set of sensors (temperature, slip, limit, level),
manual crane for the matrix and rollers,
internal magnetic separator,
grease (45kg or 180kg),
tool kit,
technical and operational documentation.
Optional equipment for granulators
electric crane for the matrix and rollers,
matrix assembly support unit,
remote roller adjustment unit ( ARGAS ),
independent system for feeding the raw material to the granulation chamber,
LCD control panel,
hydraulic belt tensioning unit,
What are the most important factors that determine the success of modern manufacturing companies? In the rapidly changing industrial sector, technological innovations and efficiency of production processes set new standards of efficiency and quality. Companies that focus on advanced solutions in their production lines, such as granulators and pelletizers, play an important role in shaping the future of the biomass and other materials processing industry. NPT Nawrocki products, with particular emphasis on the GR granulator series, are an important point of reference for every company that strives to maximize its operational efficiency while maintaining the highest standards of safety and reliability.
Pellet and feed granulators
Does the cost and technological efficiency of modern production equipment play a role in increasing the competitiveness of enterprises? In the context of pellet and granulate production, the answer to this question becomes fundamental. It is therefore worth taking a closer look at the innovative solutions presented by NPT Nawrocki, which have a direct impact on the efficiency, safety and economic efficiency of the production process.
NPT Nawrocki has gained recognition on the market thanks to its high-quality machines, such as the GR series granulators, which combine advanced technology and operational reliability. These models, such as the GR1 and GR2, are equipped with modern control systems based on computer algorithms that monitor the operation of the device in real time. The systems not only increase production efficiency, but also minimize the risk of failure and human intervention, which is important in the context of operating costs and the need to ensure production continuity.
GR granulators are characterized by a high degree of automation. Computer-controlled, they automatically adjust operating parameters to existing operating conditions. If a deviation from the programmed standards of even 1% is detected, the system immediately initiates procedures aimed at preventing damage to the machine. Such functionality not only ensures optimal use of raw materials, but also reduces the risk of downtime and related losses.