Coolers for feed, granulate and pellets
Reduction of temperature and moisture of feed and pellets. Increase of pellet strength.
2OCP coolers are an essential element of every industrial pelleting line. NPT manufactures a complete range of counterflow coolers for pellet feeds and pellets from other raw materials. The efficient operation of the cooling system allows the pellets to be cooled to a temperature of only 5C - 10C above the ambient temperature. In addition, the pellets become resistant to mechanical damage. The reduction of humidity increases the calorific value of energy pellets (from forest biomass, agricultural biomass, RDF/SRF/ASR, etc.).

Advantages of feed and pellet coolers
Modern and safe design of the pellet cooler
Anti-corrosion acid-resistant steel construction: cover, walls, discharge, fire protection mechanism, air outlet
Smooth internal surfaces: eliminate the possibility of pellet retention and the initiation of putrefactive processes contaminating feed (or other raw materials),
Durable mechanical construction guarantees long-term use,
Minimizing external surfaces where dust and dirt can accumulate and are difficult to clean,
Quick and thorough cleaning of all interior and exterior surfaces,
Complete emptying of the cooler from individual feed mixtures,
The minimal gap between the moving and fixed floors ensures tightness and uniformity of cooling and drying, also for microgranules of 1.8 – 2.2 mm.
Large inspection doors allow easy access to the interior,
The standard equipment includes a self-propelled aspiration lock made of acid-resistant steel.
It is possible to adjust the shape of the discharge to individual requirements,
The standard discharge height can be changed upon request,
On request, an individual service platform with stairs,
Integration with a crusher (tandem operation) allows for a reduction in the required height of the cooling and crushing unit.
Granulate spreader in the cooler chamber
Standard equipment in coolers with a floor from 2.4x2.4 m
Each cooler can be equipped with a granulate spreader,
Guarantee of even distribution of granulate over the entire surface of the cooling table,
Dual drive and simple, durable design ensure long service life
Easy service with access through inspection doors.
Complete system for removing humid air from the radiator
Air flow regulation: fans controlled by an inverter or manual air damper,
Efficient and economical fans with power from 5.5 kW to even 45 kW,
Stainless steel pipes with a diameter of 400 mm to 900 mm, flange connection,
Single cyclones made of acid-resistant steel with an aspiration lock,
Insulation of pipes and cyclone (insulating mat) protects the installation against water precipitation in the event of temperature differences (there is no need to use expensive air heaters),
Roof vent made of stainless steel.
Pneumatic floor and discharge drive
Possibility of optimal regulation of the cooling degree and humidity reduction,
Possibility of programmable adjustment of the floor gap size (3 programs available in AIAC )
Possibility of optimal adjustment of the cooling time of individual mixtures
feed or other raw materials guarantees optimal post-granulation processing
Work in continuous mode (instant dump) or step mode,
The floor and the cooler grate are designed to prevent the crushing of the pellets. This increases the efficiency of the entire pelleting line by significantly reducing dust and screenings,
The floor feed drive is implemented by 2 pneumatic actuators,
In the event of a power failure, the dumping mechanism automatically closes, protecting the next device from being buried.
Electric drive version available.
Work and production safety
Endress+Hauser cooling chamber level sensors (3 pcs.)
Level sensor at the hopper outlet,
One level sensor in the cooling chamber with adjustable mounting height,
Temperature sensor of the discharged medium [mounted in the floor],
Radiator Surrounding Air Temperature Sensor
Inductive inspection door opening sensor [coupled with line visualization],
Lock motion sensor,
The air outlet temperature sensor signals a possible fire hazard,
Air temperature sensors inside the chamber [depending on the chamber size: 2 or 4] coupled with the MBS vacuum transducer,
Fire-fighting air damper with immediate air intake cut-off reduces the possibility of fire spreading to a minimum,
The pneumatic air damper drive works even when the power is cut off,
Water extinguishing system (manual or automatic) with two spray nozzles,
The discharge hopper can be equipped with a flow scale that provides real production volume values.
Design and production in accordance with CE and ATEX safety standards,
The explosion-proof membrane protects the granulation line and operators against uncontrolled explosions,
The AIAC system reacts immediately in the event of temperature exceedances and initiates emergency procedures.
Technical data of NPT counterflow coolers

Chłodnica 2OCP-11 z kruszarką
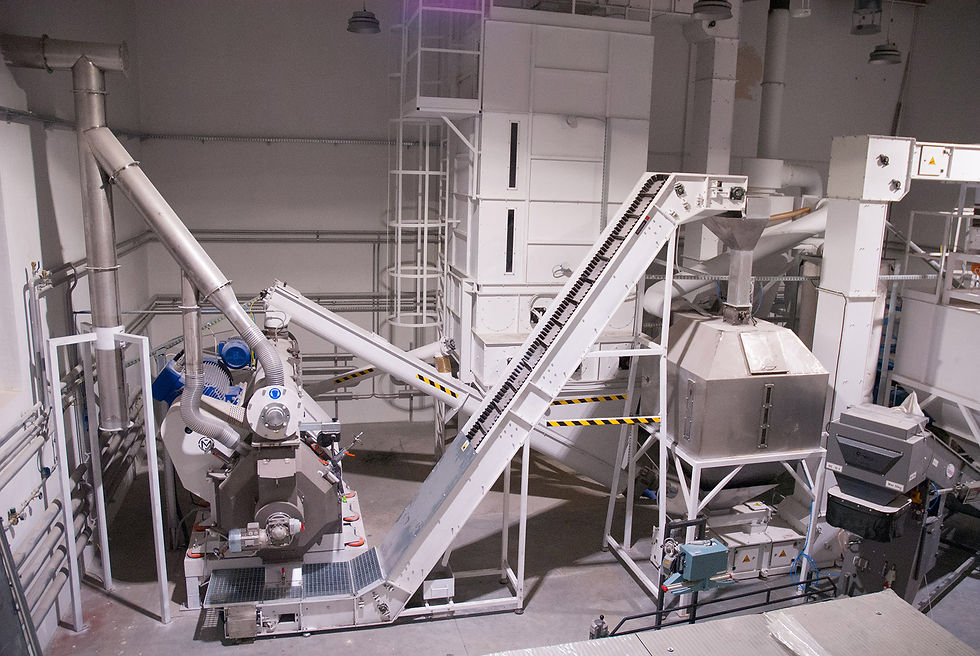
Fabryka pelletów z chłodnicą do 1 t/h

Chłodnica dla pasz ze zintegrowaną kruszarką

Chłodnica 2OCP-11 z kruszarką
How to achieve a balance between high efficiency and ecological responsibility in the production process? This is a question that many feed and pellet producers face as they strive to optimize their production lines while minimizing the impact on the environment. In response to these challenges, NPT Nawrocki offers technologically advanced pellet coolers that not only increase the efficiency of industrial processes, but also ensure their safety and durability. By offering innovative solutions such as counterflow cooling systems, NPT Nawrocki sets new standards in the field of biomass processing.
Coolers for animal feeds and pellets
Would you choose a solution that not only increases efficiency, but also protects the environment by saving resources and minimizing waste? These are the technologies offered by NPT Nawrocki, a company specializing in the production of coolers for feed, granulate and pellets. A special position in our offer is occupied by the 2OCP model, which is the foundation of an effective granulation process in the industry.
NPT coolers are irreplaceable in every industrial plant where granulates are produced from various raw materials. Their main role is to reduce the temperature and humidity of the final product, which directly improves its quality. Thanks to the use of counter-current technology, it is possible to cool the granulate to a temperature of only 5 to 10 degrees Celsius above the ambient temperature. Such a process not only increases the granulate's resistance to mechanical damage, but also increases its calorific value.
When designing coolers, NPT places great emphasis on modernity and safety of the structure. The use of acid-resistant steel for the production of the most important elements, such as the cover, walls, discharge or fire protection mechanism, guarantees anti-corrosion and long service life of the devices. Internal smooth surfaces prevent granulate from retaining, which eliminates the risk of starting putrefactive processes that contaminate the product. Additionally, the minimal gap between the movable and fixed floor ensures even air circulation.
To maximize efficiency, the coolers are equipped with systems that ensure even distribution of the granulate, as well as quick and thorough cleaning. Thanks to the large inspection doors, servicing the devices is simple and intuitive, which reduces the time needed for maintenance and increases the overall productivity of the production line.